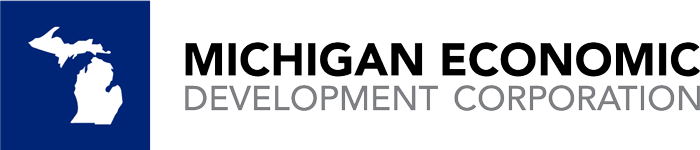
Accelerating Innovation with Industry 4.0
Courtney Overbey
Friday, March 5, 2021
Tom Kelly, executive director and CEO of Automation Alley joins Natalie Chmiko, MEDC’s VP of Pure Michigan Business Connect & International Trade for a live conversation about all things Industry 4.0.
MEDC’s Natalie Chmiko sat down to speak with Tom Kelly of Automation Alley about Industry 4.0, the impact automation is having on manufacturing, and new resources available for small to mid-sized manufacturers to adopt Industry 4.0 technologies. See below for some excerpts and key insights from their conversation and watch the full conversation to learn more.
Industry 4.0 stands for the Fourth Industrial Revolution, which at its most basic level involves the digitization of everything.
CHMIKO: A lot of people have heard of the term Industry 4.0 but may not know what it means for their business. In the most basic terms, how would you define Industry 4.0 and could you give us some examples of the types of technologies it involves?
KELLY: Industry 4.0 is a term that came out of Germany and it really stands for the Forth Industrial Revolution. The First was steam. The Second Industry Revolution Michigan invented – it was Henry Ford and the assembly line meeting Thomas Edison and the electric motor, and that changed manufacturing. The Third Industrial Revolution was when computers and robots came on the scene at the same time – mechanization along with automation. And now we are in the Fourth and the Fourth is the digitization of everything.
Michigan created and owned the Second and the Third, so we’ve built trillions of assets over 100 years based on assembly line manufacturing and mass manufacturing. And we are now moving to a world of mass customization, and products of one and 3D printing, which is the exact opposite of additive. And so, we all need to pay attention; that’s what Industry 4.0 is: focusing on how you digitize and come up with new business models.
The greatest predictor of a company’s success in adopting Industry 4.0 will be its culture.
CHMIKO: What is the biggest barrier for our manufacturers to adopt Industry 4.0 technology and what can we do to help them?
KELLY: What’s interesting is that Industry 4.0 is a technological problem; there is all these new technologies. Think artificial intelligence, 3D printing, virtual reality, augmented reality, advanced materials, big data – all of these technologies. Any one of them can be disruptive, but when they are all taken together they really cause fits for manufacturers because they have to focus on all these things. But it’s not the technology we tell people to focus on.
The most important thing that will be the predictor of your success is culture. Do you have a culture of learning? Do you have a culture of tolerance? And failure? That you are tolerant of taking risks and failing and understanding that this Industry 4.0 transition is all about learning and becoming educated and moving fast and being tolerant of failure. In manufacturing what makes that so difficult is that we were taught for 40 years that you lean out your process, that you don’t have any waste whatsoever, everything is super-efficient. You don’t risk, because risk means scrap. And here comes this overlay of Industry 4.0 that says risk and innovation is all your going to have going forward because the capital and system you have put in place to have competitive advantage to this point are going to begin to breakdown.
You have to adopt a culture of learning and you have to build a culture of trust that allows people to take risks and fail because the world is moving too fast for you to just manage a process.
You don’t have to bet the farm; manufacturers of all sizes can begin taking small steps now to adopt these technologies.
CHMIKO: Take baby steps with this. You don’t have to take huge chunks out of this all at once and just try and get the information that you can.
KELLY: We call it option-like bets. We say change your culture, and then as you allow people to take risks – we’re not talking about betting the farm. Small manufacturers say to me all the time, Industry 4.0 that’s for the big guys. They got lots of money, they got an R&D budget; we can’t get started. And I say that’s bologna. There are sensors that exist now that are $20 – they measure heat, vibration, current, all kinds of things. Put it on a machine, any machine, and hook it up to your phone and then see what that data tells you. There is no excuse, there is no budget too small for you to get started collecting data and seeing what’s happening…and keep taking those baby steps.
No one manufacturer can go it alone. It takes a community approach to be successful.
CHMIKO: Does MEDC and Automation Alley help bring manufacturers, academia and Industry 4.0 vendors together on pilot projects?
KELLY: No manufacturer has the capability to understand all of the dynamic changes that are occurring among all of these technologies at the same time. It’s way too difficult. You need a community, you need a village to help you understand and make sense. You work on AI over here in a pilot and this pilot group is working on 3D printing. We have multiple pilots going, and multiple roundtable groups talking about issues.
CHMIKO: Are there resources we can be sharing with our schools?
KELLY: We work with deans of engineering departments to help them tell their stories of the schools that they are in charge of. What is it about your engineering group that is unique? Because schools tend to specialize, or they have academic professors that are maybe very good at robotics but maybe not so good at materials. We want to tell those stories because we want to marry industry with academia.
On the student side – with the pilot we are working on with Project DIAMOnD, these are all small manufacturers that don’t necessarily have the design capabilities in-house. And what we are saying is why can’t we marry them with students in classes all over Michigan. Students would love to work on real world problems. The manufacturer knows what they want to do, marry them with students in academic who say ‘let us help you design this actual part and we will make it 3D printing ready.’ This is a pipeline that can never occur otherwise because the little manufacturer doesn’t know how to find that student. And the student doesn’t know how to find that little manufacturer. So what do they do? They end up taking a job out of state with some big manufacturer somewhere else, never to return. We need to build a pipe that is sticky for the talent we have.
Technology is the business model.
CHMIKO: We are working really closely on this statewide initiative to help these businesses prepare for these transformations. Can you talk a little bit about our effort?
KELLY: We want to take the barriers away, and say I don’t want to hear any excuses of why you can’t get the knowledge you need to make great decisions to change your business model to align with digitization of everything. You need a digital mindset that happens to overlay on a physical business. If you think about people like Mary Barra from GM, she said ‘I hope when I retire that people will view GM as a tech company that happens to make cars.’ Jamie Dimon said, ‘Today, we’re a tech company that happens to be in the finance and banking industry.’ It doesn’t matter how big or small you are, you must be a tech company that happens to be in manufacturing. This is the thing that people are not paying attention to. So, I’m super excited about the fact that if you are manufacturer come on in and let’s start sharing this knowledge with you.
CHMIKO: How should a small company present and explain this opportunity to its board or its entire company?
KELLY: If you think about society around the world, people who are CEOs and high management positions – whether you are a big company or a little company – they typically tend to be older, like me, or even older than me. And they were just at the cusp where they missed being technology natives. They view technology as a tool that is used to affect the business model they are trying to run. And that is fundamentally flawed. It’s not true anymore. Technology is the business model.
Every single company in the world needs to be a digital company first that happens to be in the business of X. If you flip it on your head and you think you’re in the business of X that happens to use technology it’s going to be a rough row to hoe for a long time. Because its only going to get more and more difficult for you to eke out a profit as the technology changes the business model and how you have to go to market to be profitable. You’re just going to lose your competitive advantage slowly, but surely.
MEDC is building on its existing partnership with Automation Alley and the Michigan Manufacturing Technology Association to help Michigan manufacturers understand and implement advanced technologies while building a robust pipeline Industry 4.0-ready talent.
Through MEDC’s Industry 4.0 initiative, Automation Alley offers a complimentary Industry 4.0 Leadership Evaluation for Michigan manufacturers that measures readiness to adopt Industry 4.0 technologies and the Michigan Manufacturing Technology Center is supporting small and medium-sized manufacturers in a hands-on, personalized capacity to identify technologies that provide maximum improvements and return on investment.
To learn more about Industry 4.0 and how your business can access resources and support from not only the MEDC, but from other key industry experts at Automation Alley and the Michigan Manufacturing Technology Center, please visit michiganbusiness.org/industry4-0.
Contact Us
To contact a business development specialist, click here or call 1.888.522.0103.